Packing & Crating Delivery System
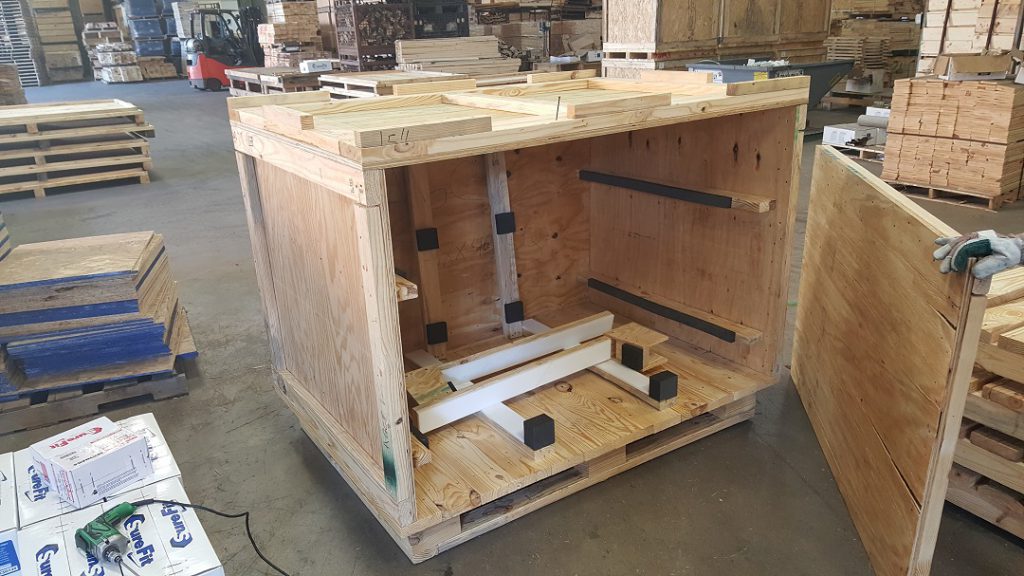
The Client Request
A manufacturer of crates and packaging was struggling to have a database solution that could help them manage the building process and material cost system for their manufacturing process. The system had specific proprietary factors put in so that the costing could accommodate price factors on materials as well as labor times regarding each and every specialty crate built. Packing crates were made to handle car manufacturing parts to ship from the part maker to the auto assembly plants. A robust scheduling and delivery system that could handle the receipt of raw materials and manufactured parts to the final delivery and shipment of the product was required.
Project Requirements
- Create Cut Sheets for Crate Builds
- Monitor and Inventory Packing Materials
- Labor / Manhour Estimator
- Billable cost factor for profit analysis
- Track Cost / Quantity of Parts Shipped
- Provide exact costs of materials per crate
- Optimize crates for part shipment quantity
- Accounts Receivable / Payable
- Inventory Management
- Scrap Wood Utilization
- Cost reduction of materials
- Transport Scheduling for Pickup/Delivery
- Multiple site database connections
- Technical minimal skilled employees’ interface
The Challenge
This packing and delivery system product required some specialty factors to include pricing, cost of material, labor factors and pricing adjustments based on receipt of goods and wage increases. Producing a unique formula design for optimal cutting of sheet goods and lumber to create crates based on unique sizes as well as scrap utilization became a hallmark of this project. Specialty small business formulas were employed to create a billing model that built in profitability per crate / labor hour. The interface needed to be extremely simple as users had little to no computer skills. Scheduling for any company without robust software can be a huge challenge. This company had multiple packing crates of parts going in and out as well as receiving parts from the manufacture. The Scheduling component had to be top of the line to ensure that they could easily receive and transmit every step of the process from receipt of raw materials to final product.
The Phoenix Solution

Creating an optimal and easy to use interface that does complex calculations and inventory management is a forte of Phoenix Consultants Group. We developed an elegant interface; rules coded into the interface to avoid employee mistakes and increased this company’s profitability by 20% and reduction of waste greater than 75%. The packing and delivery system integrated user/database security roles requirements, dirty / clean computer areas as well as hardware interactions of bar code readers to speed up the entering of data.
Company Size
< 10 employees
> 5 Corporate Fortune 500 Clients